Porosity in Welding: Identifying Common Issues and Implementing Finest Practices for Prevention
Porosity in welding is a prevalent issue that commonly goes unnoticed until it causes significant issues with the integrity of welds. In this conversation, we will discover the key elements contributing to porosity development, analyze its harmful effects on weld efficiency, and go over the finest practices that can be adopted to lessen porosity incident in welding processes.
Usual Root Causes Of Porosity

An additional regular perpetrator behind porosity is the presence of pollutants on the surface of the base steel, such as oil, oil, or rust. When these impurities are not successfully eliminated prior to welding, they can vaporize and become trapped in the weld, causing flaws. Using filthy or wet filler materials can introduce contaminations into the weld, adding to porosity problems. To reduce these usual reasons for porosity, comprehensive cleansing of base metals, proper protecting gas selection, and adherence to optimal welding specifications are crucial practices in achieving high-quality, porosity-free welds.
Effect of Porosity on Weld High Quality

The existence of porosity in welding can considerably compromise the architectural stability and mechanical homes of bonded joints. Porosity creates spaces within the weld metal, weakening its overall strength and load-bearing capability.
Among the main repercussions of porosity is a reduction in the weld's ductility and toughness. Welds with high porosity degrees have a tendency to exhibit reduced effect strength and minimized ability to warp plastically prior to fracturing. This can be specifically concerning in applications where the welded elements undergo vibrant or cyclic loading problems. Furthermore, porosity can hinder the weld's have a peek at this website capacity to properly send pressures, bring about early weld failing and potential security risks in essential structures.
Finest Practices for Porosity Prevention
To enhance the structural stability and high quality of welded joints, what particular procedures can be executed to decrease the incident of porosity during the welding process? Utilizing the right welding strategy for the details product being welded, such as changing the welding angle and weapon setting, can even more prevent porosity. Routine inspection of welds and immediate removal of any kind of concerns identified throughout the welding procedure are important techniques to avoid porosity and create high-quality welds.
Value of Appropriate Welding Methods
Applying correct welding methods is vital in making certain the architectural stability and top quality of welded joints, building upon the foundation of reliable porosity avoidance steps. Welding methods directly affect the general stamina and toughness of the welded structure. One vital facet of appropriate welding strategies is preserving the proper warmth input. Extreme heat can result in increased porosity as a result of the entrapment of gases in the weld swimming pool. On the other hand, insufficient warm may result in insufficient combination, developing potential powerlessness in the joint. Additionally, using the ideal welding specifications, such as voltage, current, and take a trip speed, is critical for accomplishing audio welds with minimal porosity.
Furthermore, the choice of welding process, whether it be MIG, TIG, or stick welding, ought to line up with the certain demands of the job to make sure ideal results. Proper cleaning and preparation of the base metal, along with choosing the ideal filler product, are likewise vital components of proficient welding strategies. By sticking to these finest practices, welders can lessen the threat of porosity development and produce premium, structurally audio welds.
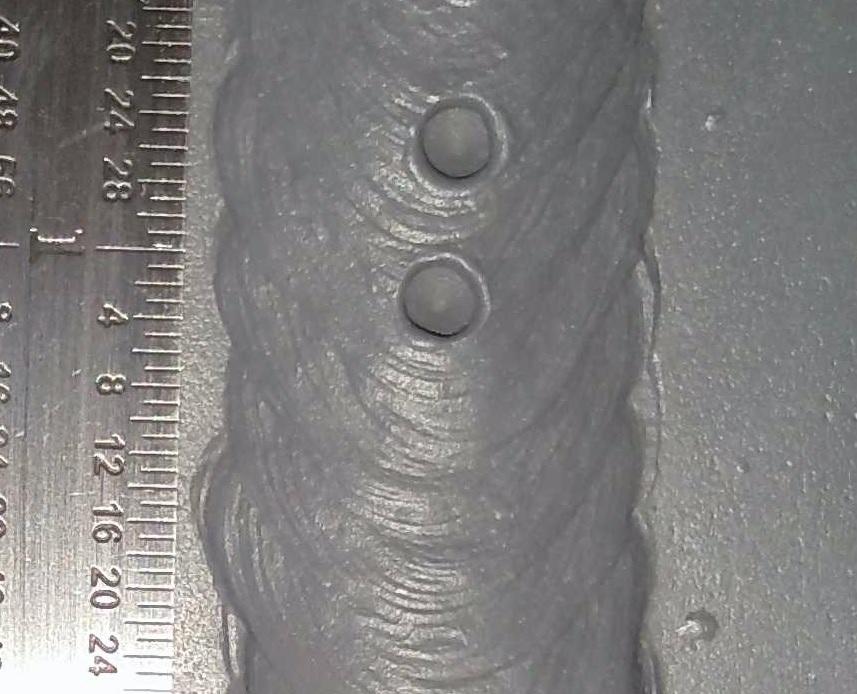
Testing and Quality Control Actions
Checking treatments are necessary to spot and protect against porosity in welding, ensuring the stamina and resilience of the last item. Non-destructive screening approaches such as Check This Out ultrasonic testing, radiographic testing, and aesthetic examination are typically utilized to determine prospective flaws like porosity.
Post-weld inspections, on the other hand, evaluate the final weld for any kind of defects, including porosity, and confirm that it meets specified standards. Executing a detailed high quality control strategy that consists of thorough screening treatments and examinations is extremely important to reducing porosity concerns and making certain the overall quality of bonded joints.
Final Thought
In final thought, porosity in welding can be a typical issue that influences the top quality of welds. By identifying the usual root causes of porosity and implementing ideal practices for avoidance, such as appropriate welding techniques and screening procedures, welders can guarantee high quality and trusted welds. It is important to prioritize avoidance methods her latest blog to lessen the occurrence of porosity and maintain the honesty of welded structures.